P
R
O
J
E
C
T
0
1
再処理工場における
「新保全プログラム」の構築
求めるのは、全ての機器が
安全に安定して動くこと
再処理工場には約40万もの機器が存在する。それら全てを安全に稼働させるには、定期点検などの保全が欠かせない。保全には現場での点検作業のほか、計画立案、体制構築、ルール管理など多くの考慮すべき要素がある。再処理工場において、これらの保全活動の総括を担うのが保全技術部だ。
2017年、あるトラブルをきっかけに、再処理工場にまつわる「新保全プログラム」を構築するプロジェクトが発足した。期間は2年半。そのあいだに約40万の機器全ての状況を把握し、技術的根拠に基づいた点検計画を作成しなければならなかった。
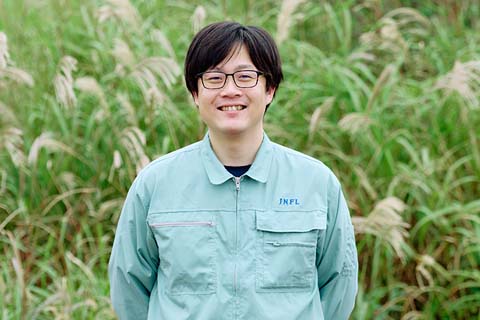
松本 康平
再処理事業部 再処理工場 保全技術部 保全技術課
2017年入社
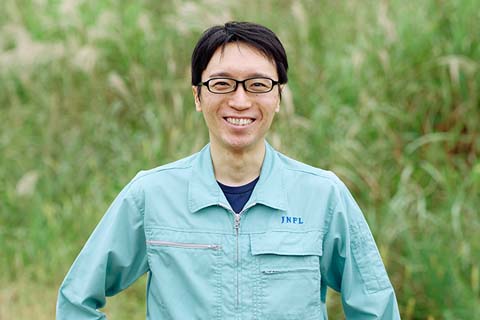
髙見 準
再処理事業部 再処理工場 保全技術部 保全計画課
2008年入社
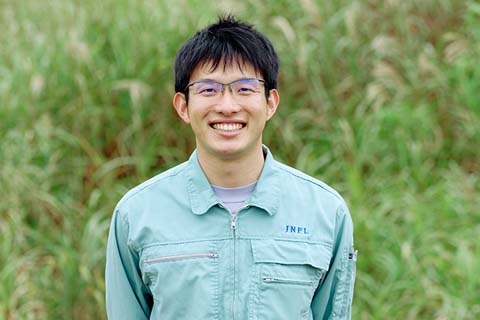
川村 優文
再処理事業部 再処理工場 保全技術部 保全計画課
2010年入社
原子力発電所に向けて定められた規定を、
再処理工場に落とし込む
再処理工場において、その運転と保全は車の両輪ともいえる。1993年の再処理工場着工から、2006年のウラン試験の完了、アクティブ試験の開始を迎えられたのも、保全の支えがあってこそ。今後の竣工ならびに安全かつ安定な操業を迎えるためにも、保全が有効に機能することが不可欠だ。
しかし、40万にもおよぶ機器の健全性を維持することは容易ではない。機器は使用開始から年数が経過するにつれ経年劣化が進行するため、一つひとつの経年劣化を考慮した保全を実施する必要があるからだ。そこで、日本原燃は原子力発電所で使われている保守管理規定「JEAC4209」をベースとした、新たな保全プログラムの構築に動き出そうとしていた。
- 川村
- それまでの「メーカー推奨主体の点検」を止め、事業者自ら「機器の構成部位ごとに有効な保全内容を考える」ように変わる必要がありました。自動車に例えると、ディーラーに点検を丸投げするのではなく、「ブレーキパッドはすり減るから定期的に交換する」などを考えて、点検するということです。さらに、その保全が妥当だったかの振り返り、改善も求められます。この計画から改善までの流れをサイクルとして繰り返すのが、JEAC4209の考え方です。
JEAC4209に基づく新保全プログラムの検討は、2015年より本格化する。検討メンバーに選ばれた川村は、「全てがゼロからのスタートだった」という。
- 川村
- それまでの部署では保全に関与していなかったため、最初はJEAC4209の冊子を読み解き、保全について学ぶ日々でした。JEAC4209は原子力発電所向けに定められた規定ですが、再処理工場には発電所にない特有の機器が多数あり、化学薬品を使用するなど、施設の特徴も異なっていました。そのため、JEAC4209の考え方を再処理工場で使えるものとするために、様々な検討をする必要がありました。
検討を進めながら、実際に点検作業を担う現場担当者にも、新たな保全プログラムの方針に理解を得なくてはならなかった。なぜ、今まで良しとされていたルールを変えねばならないのか、現場のベテランにも納得してもらうために、川村ら検討メンバーは真摯に説明を繰り返した。
ところが2017年8月、事態が大きく動く。非常用発電機が設置されている施設に、雨水が浸入するトラブルが起きたのだ。燃料供給用の配管が通る空間に雨水が溜まり、壁にしみ出したのが原因だった。機器の管理が行き届かず、必要な点検がなされていなかったことは保全上大きな問題となり、ニュースにも取り上げられてしまった。
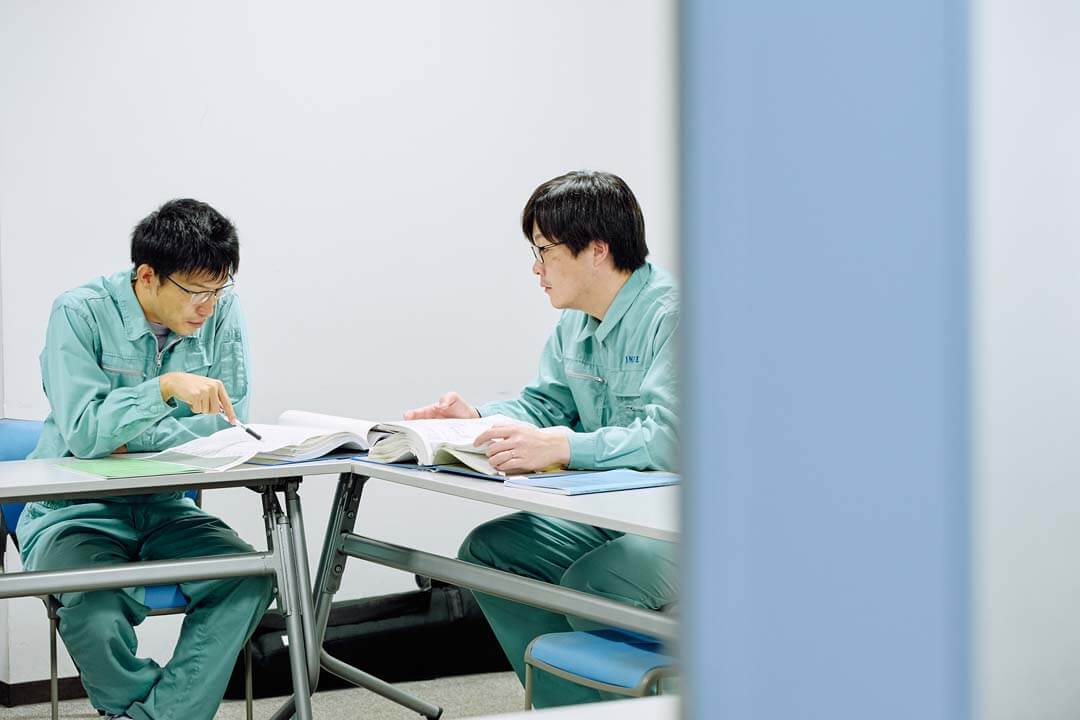
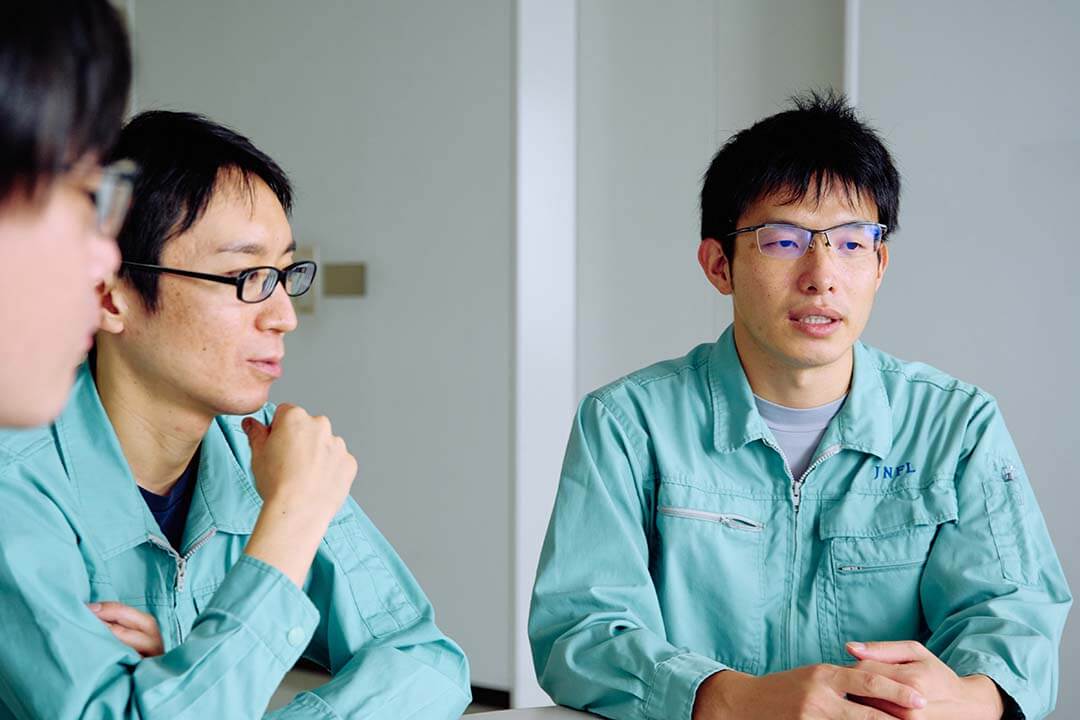
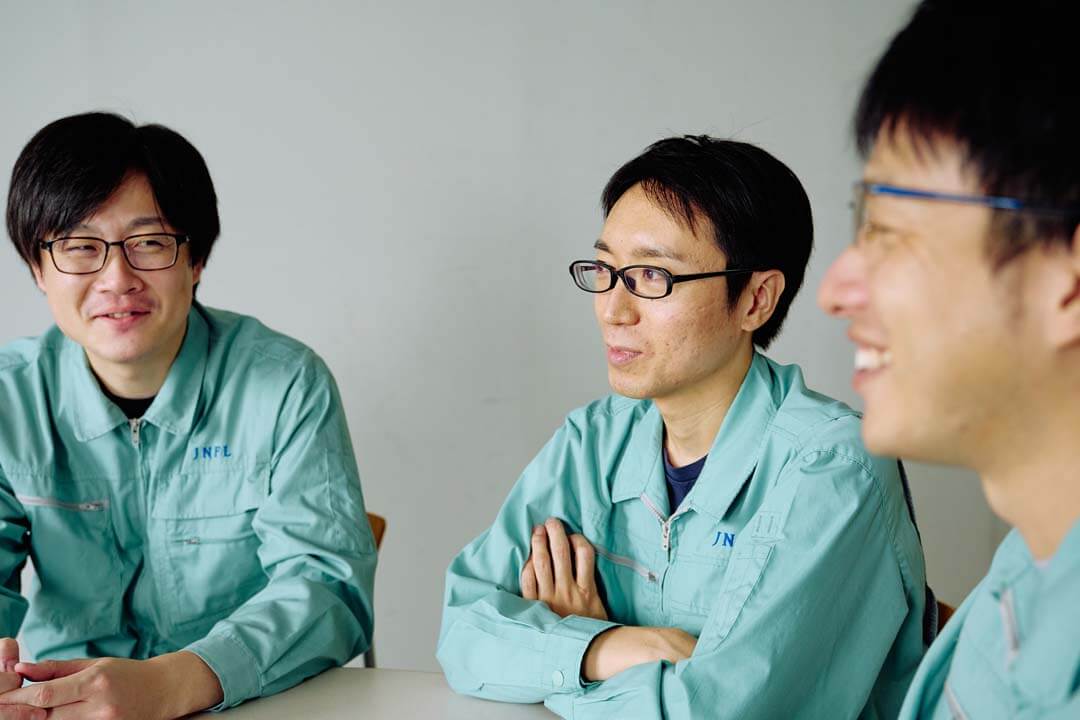
約40万ある機器全ての状況を把握する
非常用の施設に雨水が浸入するトラブルを踏まえ、保全に関する問題の解決が再処理工場の最優先事項となった。竣工に向けて進めていた新規制基準に係る適合性審査の対応をストップし、事業部が一丸となってこの問題に取り組む必要があった。
すぐにプロジェクト全体を統括する事務局が設置され、事業部内からメンバーが集められた。放射線管理部に所属していた髙見もその一人だ。
- 髙見
- 保全は未経験の分野でしたので、当初は私に事務局が務まるのか非常に不安でした。ですので、保全部門のメンバーはもちろん、他部署や電力会社の方々にも協力いただきながら、まずは「目指すべきゴール=目標」を定めていきました。一つ目の目標は、他に管理が行き届いていない機器がないか、また安全に影響するような状態がないか把握すること。二つ目の目標は、全ての機器を適切に保全できる状態にすることです。それは川村らが取り組んできた新保全プログラムを構築することであると考えました。
プロジェクトの計画は、再処理工場内にある全ての機器を把握する「第1ステップ」と、その結果をもとに新保全プログラムを構築する「第2ステップ」の2つに分かれていた。第1ステップでは、再処理工場内の全ての部屋や敷地を歩いて確認する「ウォークダウン」が行われた。
- 髙見
- 再処理工場の敷地は広大で、建屋には何千もの部屋が存在します。約40万ある機器にも様々な種類があるので、各部署から電気、機械、土木などの専門家を集めてウォークダウンの班を構成しました。機器の確認にあたっては、経験によるバラつきが出ないよう、機種ごとに確認ポイントを整理して臨みました。
歩いて行けるところは全て訪れ、目視で確認を進めていく。しかし、建屋内では高所に設置された機器もあった。全ての箇所に足場を設置していては間に合わないため、高所カメラによる確認を導入するなど、効率的なやり方を常に模索した。
- 髙見
- 当初は確認結果を紙に記録し、現場から戻った際にデータベースへ入力していました。しかし、記録が膨大な量になるため、途中からタブレット端末を導入し、その場で直接入力できるようにしました。また、建屋外の機器については、ドローンを飛ばして広域を確認するなど、どんどん作業を効率化していきました。
また、プロジェクトを統括する事務局では、進捗状況の確認や、課題への対策検討、各事業部との連携など、マネジメント業務も多岐にわたる。社内でも重要プロジェクトと位置づけられていたため、上層部への報告や、原子力規制庁への説明も求められた。膨大な作業量を前に、髙見は一つひとつ粘り強く対応していった。
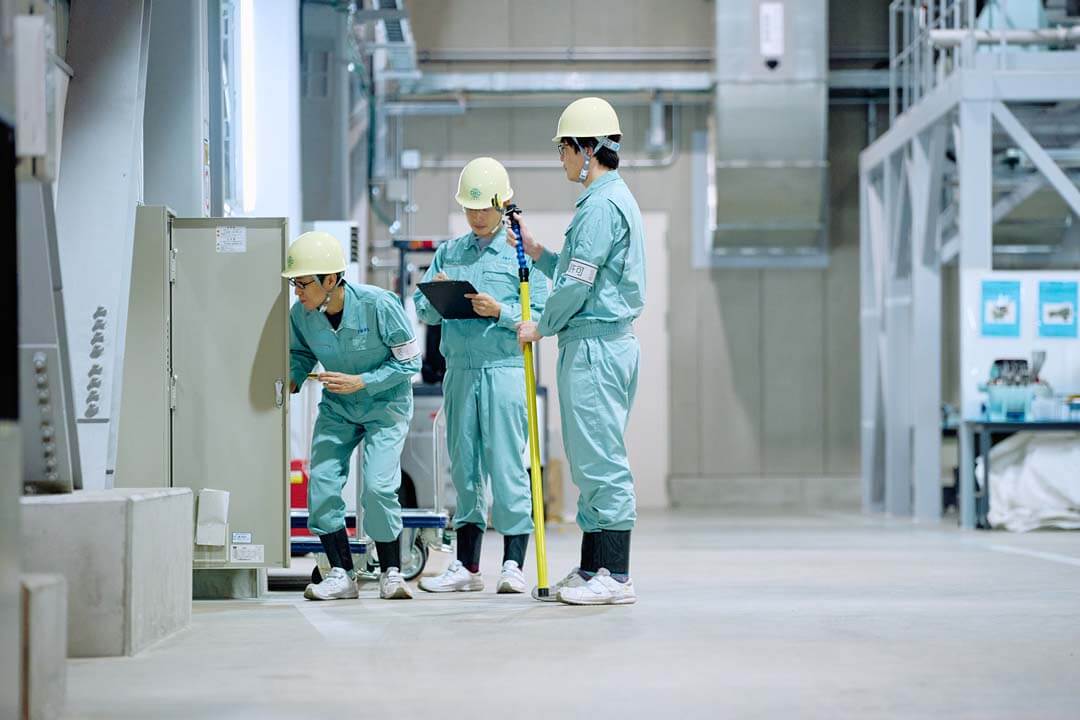
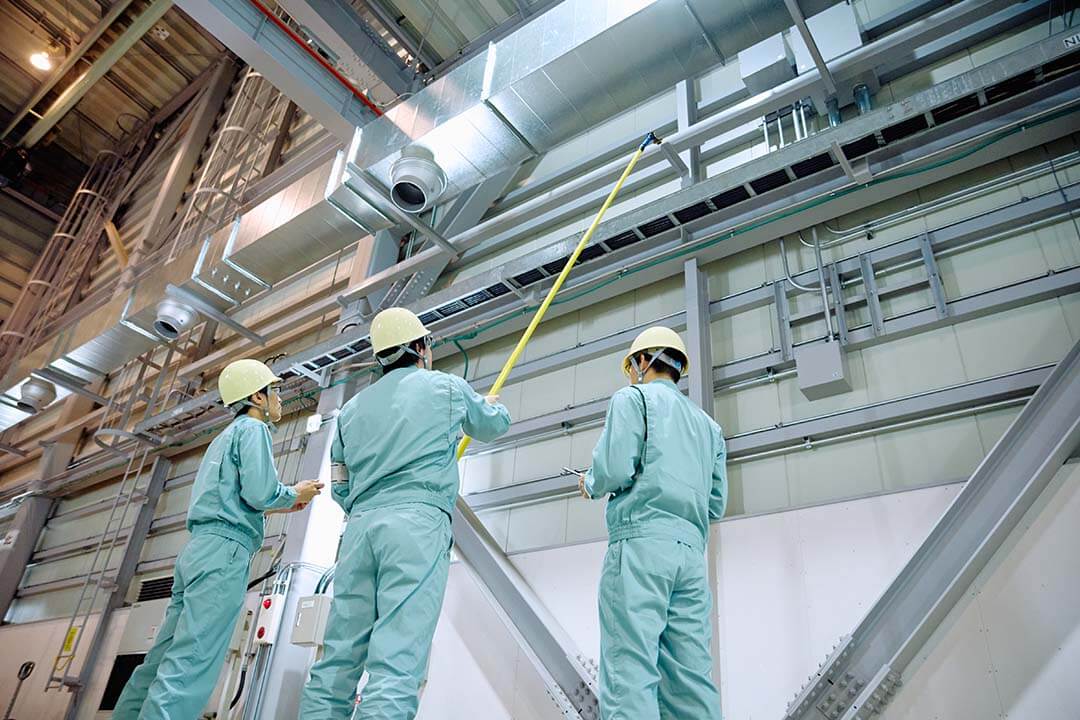
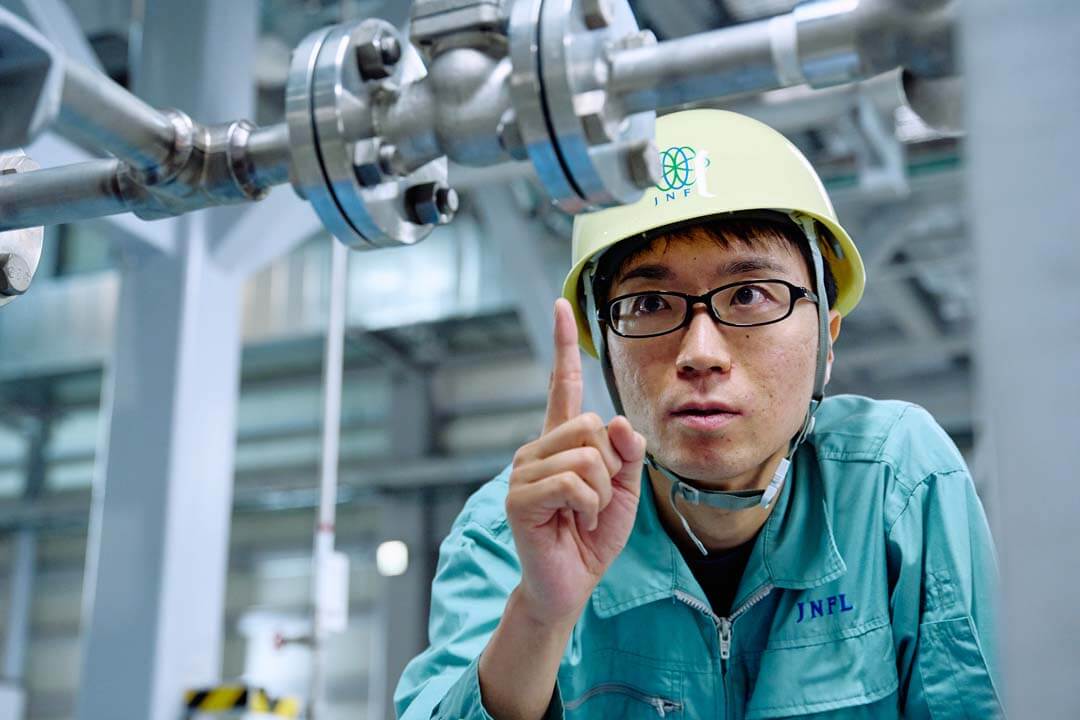
現場の理解なくして、
最適な保全はありえない
プロジェクトが第2ステップに入ったのは、2019年度。残り1年で、JEAC4209をベースとした新保全プログラムを完成させねばならなかった。
- 川村
- それまでの当社のルールには、保全業務としてのPDCAサイクルが明確ではありませんでした。具体的にはPlan(点検計画)とDo(点検実施)が中心で、Check(点検結果の確認・分析)とAct(改善策の検討)が弱かったのです。JEAC4209ではPDCAそれぞれの項目について明確化されており、同じ水準の内容を新保全プログラムのルールに反映させる必要がありました。
2017年に入社した松本もまた、新保全プログラムの構築に携わった一人だ。配属後すぐに本プロジェクトに入り、先輩のサポートをしながら仕事を覚えていった。プログラム構築にあたっては、川村ら先輩社員からJEAC4209のエッセンスを学んでいった。
- 松本
- 現場経験がないままルールをつくることになるので、現場の声を聞くことを重視しました。現場の方々のところに足を運び、「今まではこうだった」「こうしてくれたらやりやすい」といったコメントをもらって、可能な限り現場の意見をルールへ反映できるように努めました。
プロジェクトの第1ステップでは、把握した機器全てに対し、新たに経年劣化を考慮した点検計画の作成が行われた。ただ、約40万の機器、しかもその部位一つひとつに対して、どのような劣化が生じ、どのような保全が有効か検討していては、いくら時間があっても足りない。そこで、型式や材質、環境条件などで機器を「グルーピング」し、グループごとに点検計画を検討していった。
- 松本
- 原子力発電所や一般産業でも使われている汎用的な機器は、グループごとに点検計画を作成することが可能でした。しかし、一部の再処理工場特有の機器については、点検計画の作成にそれぞれのメーカーの設計的な知見を必要としました。対象を400機器ほどに絞り、メーカー8社と何度もやりとりを重ねて、新たな保全の考え方を理解いただきながら、点検計画を作成していきました。
さらにプロジェクトと並行して、点検計画を管理・運用するための保守管理システムの刷新も行われた。新たなシステムは新保全プログラムに沿った内容とするため、川村や松本はシステムの要求仕様の作成にも携わった。
新保全プログラムに係るルールの整備、約40万の機器に対する点検計画の作成、そして保守管理システムの刷新の3つの業務を限られた期間で進めることは困難を極めた。しかし、保全部門、情報システム部門など様々な部門の力を結集し、何とか最後までやり遂げることができた。
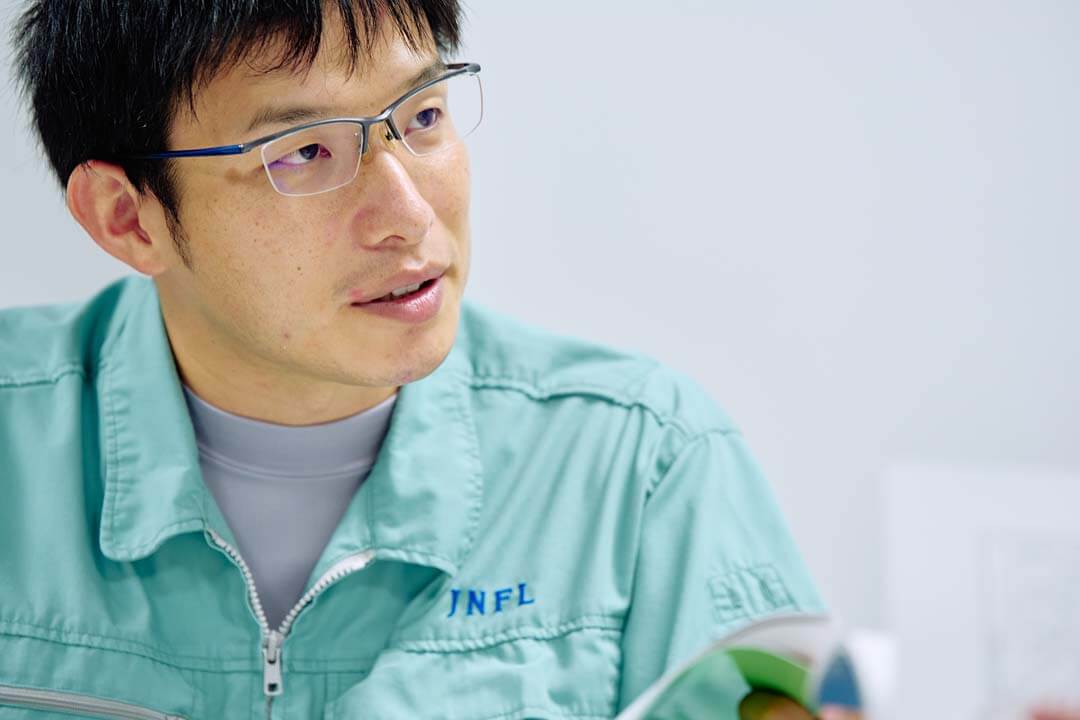
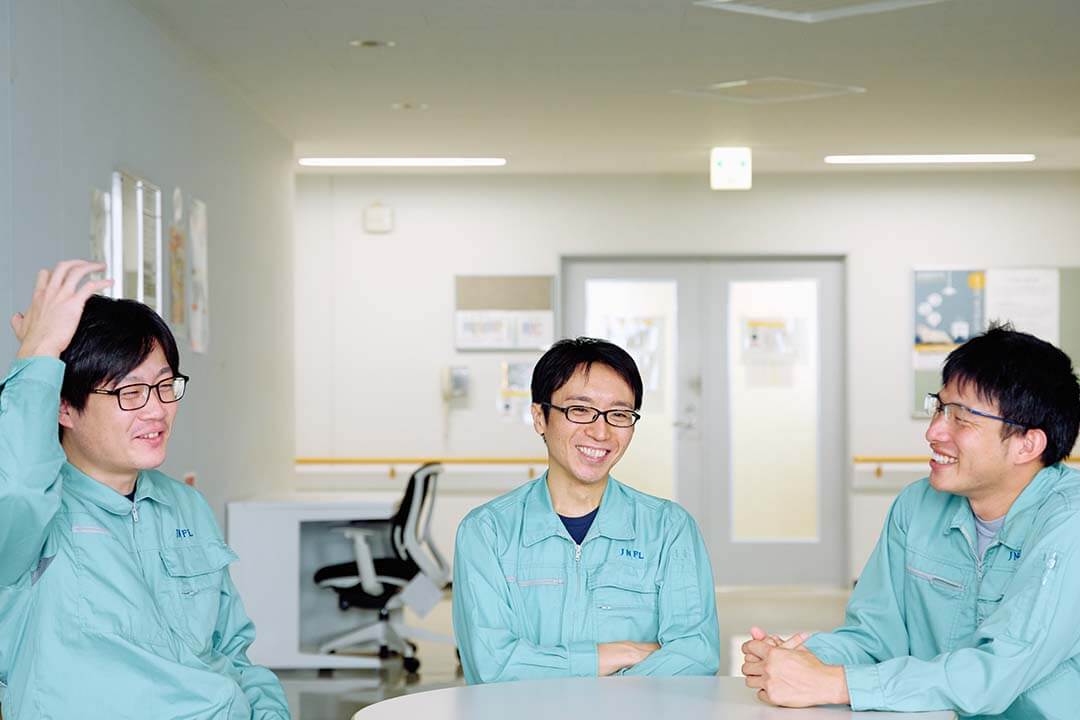
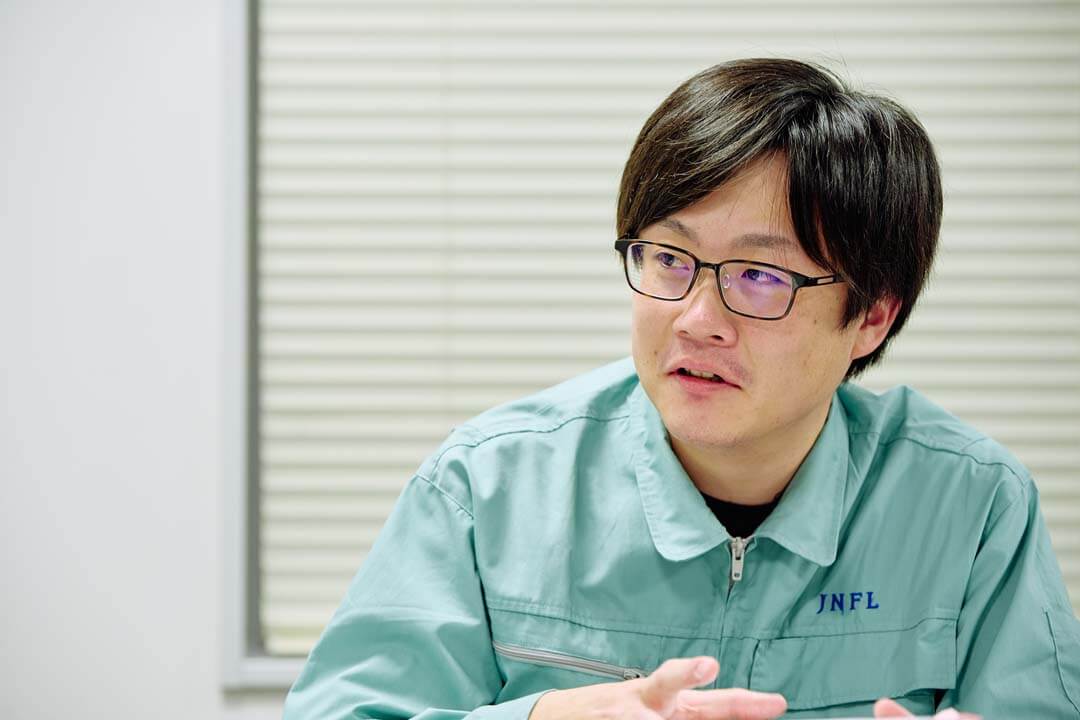
ルールを「進化」させ、
安全・安定操業を実現する
こうして、新保全プログラムに関するプロジェクトは2019年度(2020年3月)で一つの区切りを迎えた。2020年4月からは、新ルールに沿って保全活動が始まり、新しい保守管理システムの稼働も始まっている。
しかし、プロジェクトに携わったメンバーはさらに先を見据えていた。再処理工場を安全・安定に操業していくには、保全プログラムを維持管理するだけでなく、たゆまず改善を続けていかなければならないからだ。ルールは、一度つくって終わりではない。
- 川村
- プロジェクトを終えて、計画通りに点検作業を進めるには、中長期的に戦略を立てることが重要だと改めて実感しました。必要な技術力の維持や、体制の確保、コスト抑制など考えるべき要素はたくさんあります。今回定めたルールも、現場の状況次第では改訂が必要になる場合があるでしょう。トラブルを未然に防ぐためにも、中長期的な視点でこれからも保全プログラムの最適化を続けていきます。
- 松本
- 本プロジェクトでは社内だけでなく、メーカーなど社外の方々とも議論を交わしながら仕事を進めていきました。より良い保全のために、様々な考えや視点を知ることができたことは非常に学びになりました。2021年7月からは所属部署が変わり、現場部門に携わるようになりましたので、自身が携わった新たな保全の仕組みをきちんと浸透させて、現場におけるPDCAを回していきたいと思います。
- 髙見
- 当初はいつ終わるのかと思うほど大きなプロジェクトでしたが、事業部が一丸となって完遂した時は、大きな達成感を覚えました。全体を統括する役割は、大きな責任を感じましたが、自分を大きく成長させることができました。2022年の再処理工場の竣工後は、保全の重要度がますます高まるでしょう。効率的に保全を実施できる体制の構築や保全業務プロセスの改善を進め、安全かつ安定した操業を実現したいと考えています。