ガラス固化技術の確立から新型ガラス溶融炉の開発へ
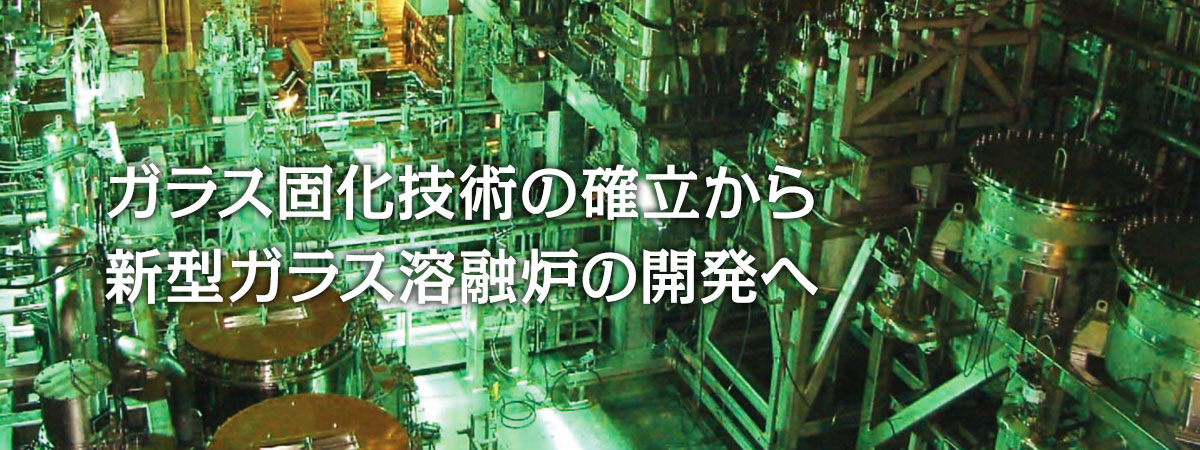
開発までの道のり
ガラス固化試験のスタート
再処理工場では、2006年3月より、しゅん工前の最終段階の試験である、実際の使用済燃料を用いたアクティブ試験を開始しました。
アクティブ試験は5つのステップに分かれ、段階的に使用済燃料の取扱量を増やし、施設の安全性や機械・設備の性能をステップごとに確実に把握しながら進め、2007年8月、高レベル廃液ガラス固化設備の処理能力の確認を含む行う第4ステップを開始。
そして、2007年11月には、最後の山場となる核分裂生成物を含む高レベル廃液をガラス固化処理する「ガラス固化試験」を開始しました。
ガラス固化体容器(キャニスター)への注入・充填を実施し、安全性の確認、ガラス固化の重要な要素である温度条件などのデータを取得しながらガラス固化体の製造を進め、確実に試験項目を消化し、運転技術の習熟・経験も積み重ねながら、順調に試験が終了するものと思われました。
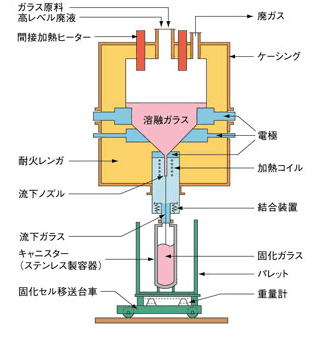
ガラス溶融炉概要図
困難との戦いのはじまり~ガラスの流下性低下~
ところが、2007年12月、ガラス溶融炉内の溶融ガラスの粘性が高くなり、流下に時間を要したことから試験を中断し、溶融炉内にある溶融ガラスを一旦抜き出す作業を実施しました。
中断した試験の早期再開に向け、溶融炉内にカメラを入れ、詳細な点検を行うとともに、残留物の除去作業などを全力で進め、2008年7月に試験を再開しました。
約半年間中断した試験を再開できたことで、焦燥感が漂っていた現場に活気が戻ったのもつかの間、試験再開の翌日、再びガラスの十分な流下を確認することができなくなり、1本のガラス固化体を製造することなく再び試験を中断しました。
その後の調査で、溶融ガラスをガラス固化体容器(キャニスター)に流下させるノズルの温度が十分に上昇していなかったため、中のガラスが冷えて粘性が高まり、流下ノズルにガラスが付着したことでノズルの出口が詰まったものと判明したことから、ノズルの温度目標値を高めに設定するといった新たな対策を行い、10月に試験を再開しました。
再開した試験では、安定した状態でガラス固化体15本を製造しましたが、さまざまな状況下での安定運転を確認するため、不溶解残渣※1を廃液に混ぜたところ、炉底部に白金族元素※2の堆積を示す兆候がみられ、徐々にガラスの流下性が低下したことから、洗浄運転※3を行い、溶融炉内の回復に努めましたが、状況が改善しないことから、炉底部に堆積した白金族元素を強制的に抜き出すため、かくはん棒を使ったかくはん運転を実施し、全力で復旧作業に取組みました。
※1 不溶解残渣 | : | 使用済燃料のせん断片を溶解槽で溶解した際、溶解せずに残る粒子状のもの。 |
※2 白金族元素 | : | 白金および白金に似た性質を持つ元素の総称。使用済燃料中のルテニウム、ロジウムおよびパラジウムは、その多くが高レベル放射性廃液に含まれ、これらが溶融炉内で沈降・堆積すると、ガラスの流下性低下の原因になる。 |
※3 洗浄運転 | : | 炉底部への白金族の堆積を防ぐため、溶融炉にガラスを追加投入して溶液中の白金族元素の濃度を薄め、洗い流す作業。 |
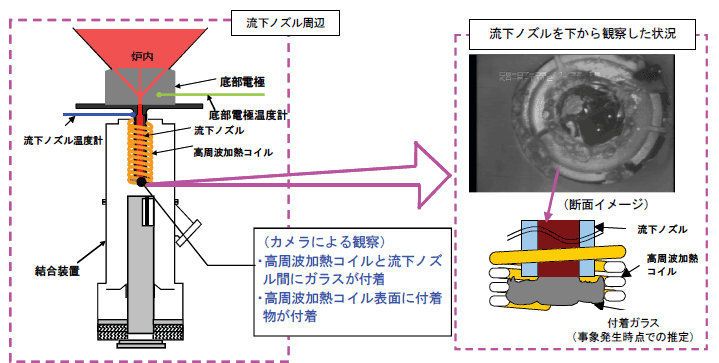
流下ノズルに付着したガラスの様子
さらなる困難との戦い~かくはん棒の曲がり、天井レンガの落下~
かくはん運転を実施中の2008年12月、かくはん棒の動きが鈍くなったことから、溶融炉内にカメラを挿入したところ、かくはん棒が曲がっていることが判明。
さらには、天井レンガの一部が落下していることも確認されました。相次ぐ困難に直面し、現場には悲壮感も漂いましたが、「ガラス固化技術を確立させるんだ!」という強い使命のもと社員が一致団結し、あきらめずに立ち向かった結果、遠隔操作によるレンガ回収装置を短期間で開発。
そして、熟練した遠隔操作員の技術により、2010年6月に落下したレンガの回収に成功しました。
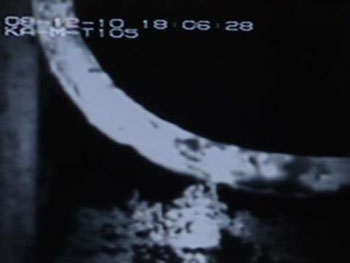
曲がったかくはん棒
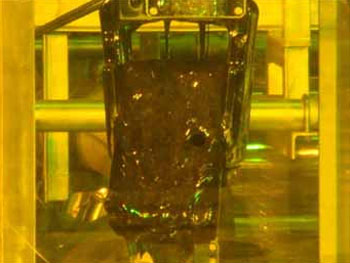
回収したレンガ
安定運転の実現に向けて
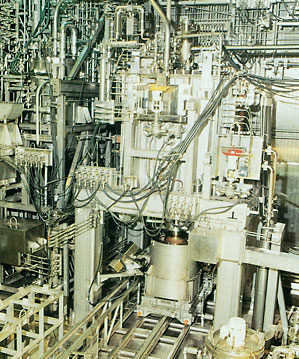
JAEA東海事業所再処理工場のガラス溶融炉
画像提供:日本原子力研究開発機構
現場でのガラス溶融炉復旧作業と並行して、試験の再開に向け、ガラス溶融炉の運転方法や設備の改善を図るため、企業や大学をはじめとする国内外の研究機関などに協力を求め、さまざまな対策を検討しました。
また、茨城県の日本原子力研究開発機構(JAEA)東海事業所にある実規模大のモックアップ溶融炉(KMOC)を活用し、約2年間かけて検証を実施。
そこで得られた知見を踏まえ、白金族元素が炉底部へ沈降、堆積しないよう溶融炉内にガラス温度計を複数追加して、溶融ガラスの温度管理を徹底すること、ガラスの流下性が悪化する前に定期的な洗浄運転を実施することなどの改善を行い、ガラス固化試験の再開にこぎつけました。
困難を乗り越えガラス固化技術の確立へ
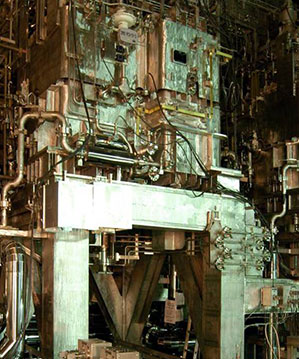
当社再処理工場のガラス溶融炉
KMOCを使用した試験では、ガラス溶融炉を運転する現場社員の技術・技能の向上にもつながりました。
2013年1月3日にB系列、そして、2013年5月26日には、最後に残されたA系列の安定運転および性能確認試験が終了し、計画していたガラス固化試験は全て終了しました。
これにより、国によるガラス固化設備の使用前検査に向け、確認すべき項目の試験は全て完了し、ついに、国内外の英知を結集したガラス固化技術を確立することができました。
ガラス固化技術のさらなる向上を目指して~新型ガラス溶融炉の開発~
2012年1月のガラス固化試験再開後は、着実に試験項目を消化し、ガラス溶融炉の安定した運転を確認することができました。
その一方で、現行のガラス溶融炉は設計上の寿命が5年であり、将来的に取替えが必要になることから、より一層の安定運転を目指して、新型のガラス溶融炉の開発にも取組んできました。
2013年10月には、研究・開発の拠点となる「ガラス固化技術開発施設」が再処理事業所の敷地内に完成。同一敷地内に建設したことで、試験で得られたさまざまな知見や成果を迅速に実際のガラス溶融炉に反映させることが期待できます。
そして、この施設には、現行のガラス溶融炉でのトラブルを乗り越えて得た情報・知見を反映させた、「新型ガラス溶融炉」の開発のほか、遠隔操作性の確証試験や運転員等の訓練も行っています。
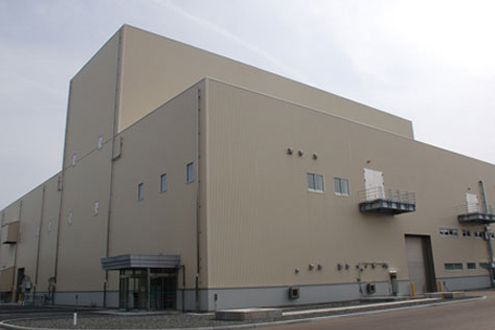
ガラス固化技術開発施設
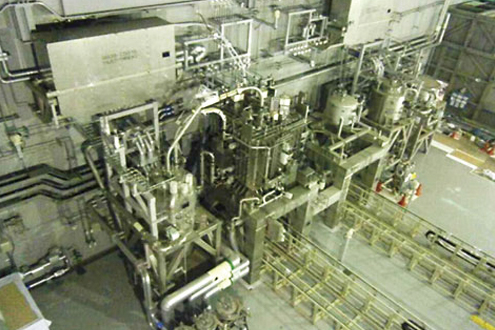
固化セル模擬室
英知を結集!前進する研究開発
新型ガラス溶融炉にとっての命題は、現行炉の課題である白金族元素の沈降・堆積を抑え、ガラスの流下性を確保することです。そのため、炉の構造や設備改善の研究に加え、ガラス固化体本数の低減や運転性の向上といった更なる性能向上を図るため、ガラス素材の開発にも取組んできました。
研究開発は電力中央研究所や日本原子力研究開発機構(JAEA)、東京工業大学、滋賀県立大学、秋田大学、IHIといった研究機関からメーカーまで、各分野のエキスパートとスクラムを組みながら、経済産業省「使用済燃料再処理事業高度化補助金」(2009~2013年度)の交付も受け、まさにオールジャパン体制で臨みました。
その結果、白金族元素の堆積などによる流下性低下の対策として、炉底部の形状を現行の四角すいから円すいに、傾斜角度を45度から60度へ大きくすることでガラスが流下しやすくなることに加え、より多くの高レベル廃液を取込めるガラス素材の開発にも見通しを得ることができました。
そして、これらの開発成果を実規模サイズで検証するためのモックアップ試験炉(K2MOC)を製作し、試験を開始することとしました。
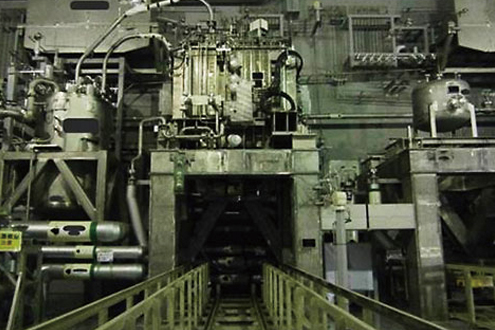
モックアップ試験炉(K2MOC)正面
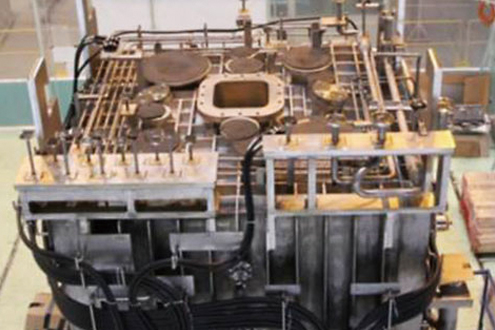
モックアップ試験炉(K2MOC)上部
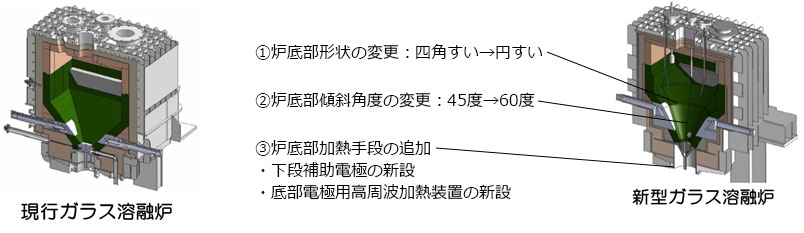
白金族元素の沈降・堆積を抑え、ガラスの流下性向上を図るために加えた主な改良
幾度も重ねた試験 その先に見えた新型ガラス溶融炉の姿
2013年11月から2014年2月にかけて、新たに製作したK2MOCにおいてモックアップ試験の第1段階を開始しました。
この試験では、ガラスを目標の温度で管理できたことにより、回数を重ねても流下性は良好で、白金族元素が炉底部に堆積した兆候は確認されず、また、ドレンアウト※4後にも、炉内のガラスは全て排出されており、残留物は確認されませんでした。
2014年11月から2015年1月にかけて実施した第2段階の前半試験では、流下性能がさらに向上していることを確認するために、白金族元素を含まない模擬廃液とガラス原料ビーズを供給した洗浄運転の間隔を拡大させるとともに、不溶解残渣などの分量を変化させて試験を行いました。その結果、洗浄運転を実施することなく、40バッチ※5運転ができることを確認しました。
これは、洗浄運転を間に挟みながら30バッチ連続運転するという当初の目標を大幅に上回る結果となりました。
洗浄運転をしなくても白金族元素が炉底部に堆積することなく連続運転できたことは、ガラス固化体の製造本数を抑制することにつながります。
2015年2月から5月にかけて実施した第2段階の後半試験では、国による使用前検査の条件である1時間当たり約70Lの廃液供給量で運転できることや、設計上の処理能力である1日4t使用済燃料を再処理した場合(800t/200日)の廃液供給量で運転ができることを確認し、試験は順調に終了しました。
※4 ドレンアウト | : | ガラス溶融炉内に保持されているガラスを全量抜き出すこと。 |
※5 1バッチ | : | ガラス固化体1本分を製造する運転のこと。 |
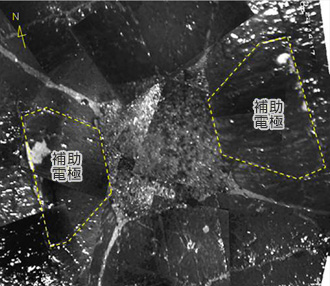
【現行炉】
2013年時点:アクティブ試験 B系列ガラス固化試験時
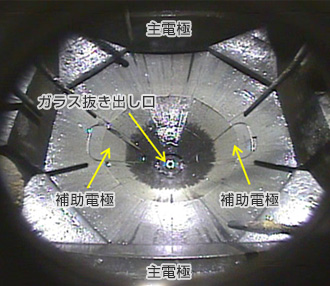
【新型溶融炉】
(第2段階(後半)試験終了後)
世界最高性能のガラス溶融炉を目指して
これまでのさまざまな試験結果から、新型ガラス溶融炉は流下性が格段に向上し、廃液の処理能力も良好で、より安定的に運転できることが確認できました。
引き続き、データの詳細な評価を行い新型ガラス溶融炉を実機への導入する判断に向けた検討を行ってまいります。
当社はこれからも、より安定的に運転することができる世界最高性能のガラス溶融炉の研究開発に挑戦し続けます。
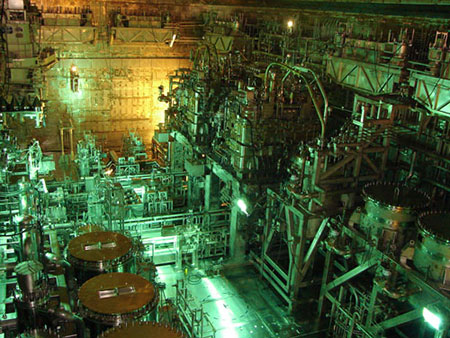
当社再処理工場ガラス固化設備
ガラス固化技術
原子力発電所で使い終わった使用済燃料を化学的に処理(再処理)すると、原子力発電の燃料として再利用できるウラン、プルトニウムのほかに、放射能レベルの高い廃液(高レベル放射性廃液)が発生。
ガラス固化技術は、この廃液をガラス溶融炉で溶かしたガラスと混ぜ合わせ、専用のステンレス製容器(キャニスター)に入れたガラス固化体を製造する技術。
ガラス固化設備のこれまで
-
- 再処理工場のしゅん工時期:
2026年度中
- 再処理工場のしゅん工時期:
- 2018
-
- 2015年2月~5月
- 新型ガラス溶融炉モックアップ試験
第2段階(後半)の実施
使用前検査の前提である1時間当たり約70Lの廃液供給量で、より安定的に運転ができることを確認。
- 2015
-
- 2014年11月~2015年1月
- 新型ガラス溶融炉モックアップ試験
第2段階(前半)の実施
目標とした30バッチ連続運転(洗浄運転あり)を上回る40バッチ連続運転(洗浄運転なし)ができることを確認。
※1バッチ:ガラス固化体1本分を製造する運転のこと。 -
- 2014年1月
- 新規制基準への適合申請
第2段階(前半)の実施
新規制基準への適合性確認等の審査を受けるため事業変更許可および保安規定変更認可を申請。
- 2014
-
- 2013年12月
- 核燃料施設等の新規制基準が施行
-
- 2013年11月~2014年2月
- 新型ガラス溶融炉モックアップ試験
第1段階の実施
ガラスを目標の温度管理で調整することができた。ガラスの流下性も、回数を重ねても良好で、白金族元素が炉底部に堆積した兆候は確認されず。
-
- 2013年10月
- ガラス固化技術開発施設しゅん工
新型ガラス溶融炉における各種試験などの研究・開発や、遠隔操作の試験、運転員等の技術習熟訓練を行い、ガラス固化技術の更なる信頼性の向上を目指す。
-
- 2013年5月
- ガラス固化試験開始・終了(A系列)
試験結果
本試験の終了により、使用前検査に向けて確認すべき全ての試験が終了。
-
- 2013年1月
- ガラス固化試験終了(B系列)
試験結果
ガラス温度や気相温度、炉底部の温度を目標の範囲内で所定のバッチ数の運転ができること、設計上の最大処理能力で運転できることを確認。
- 2013
-
- 2012年12月
- ガラス固化試験の開始(B系列)
-
- 2012年8月
- 模擬廃液を用いた事前確認試験を実施 (A系列)
試験結果
-
- 2012年7月
- 実廃液を用いた事前確認試験を実施(B系列)
試験結果
-
- 2012年6月
- 模擬廃液を用いた事前確認試験を開始(B系列)
-
- 2012年1月
- ガラス流下速度低下
高レベル廃液ガラス固化建屋ガラス溶融炉(B系列)に模擬ビーズを入れ、ガラスを流下させたところ、流下性低下事象が発生
- 2012年5月
- 原因と対策
流下ノズル部への異物発生・堆積の抑制等の対策を実施
対策実施後、流下性が回復したことを確認したことから事前確認試験へ移行。 - 2012
- 2011
- 2010
- 2009
-
- 2008年12月
- 溶融炉内かくはん棒の曲がり
かくはん棒の動きが鈍くなったことから、溶融炉内をカメラで確認したところ、かくはん棒が曲がっていることが判明。
- 2008年12月
- 経過報告
- 2008年12月
- 炉内天井レンガ一部損傷
溶融炉内をカメラで確認したところ、溶融炉天井レンガの一部が損傷していることを確認。
- 2010年2月
- 経過報告
- 2010年6月
- 落下レンガ回収
落下したレンガの回収に成功
- 2010年7月
- 最終報告
原因および対策をまとめ、調査の結果、今後の運転の安全性に問題がないことを確認。
-
- 2008年7月
- ガラス溶融炉運転性能確認試験の停止
ガラス溶融炉の運転性能確認試験を開始したが、ガラスの十分な流下が確認されず、流下操作を停止。
- 2008年8月
- 対応状況
- 2008
-
- 2007年11月
- ガラス固化に係る試験(ガラス溶融炉運転性能確認試験)を開始(A系列)
- 再処理工程で抽出した核分裂生成物を含む高レベル廃液をガラス溶融炉へ供給する作業を開始
- ガラス固化体容器(ステンレス製)への注入・充填を開始
-
- 2007年8月
- アクティブ試験の第4ステップの開始
高レベル廃液ガラス固化設備の処理能力の確認を行うアクティブ試験第4ステップを開始。
- 2007
-
- 2006年3月
- アクティブ試験開始
- 2006