<別 添>
平成14年9月22日
使用済燃料受入れ・貯蔵施設のPWR燃料貯蔵プール水
漏えい原因調査状況と今後の取り組みについて
PWR燃料貯蔵プール北壁部西側ライニング部の漏えい原因調査のため、ライニングの一部を原因調査試験片として切り出し、7月23日に社外研究施設へ搬出し調査を進めておりましたが、今般、計画していた調査が終了しました。
その結果、今回の漏えいの原因となるようなライニングに貫通した欠陥は確認できませんでした。このため、現地のPWR燃料貯蔵プール北壁部西側ライニング部溶接線について、再度調査を実施します。
以下に原因調査結果及び今後の再調査計画について報告します。
原因調査及び今後の再調査計画の策定につきましては、専門家からの指導を得ながら進めました。
1.社外研究施設における漏えい原因調査
プール下部横溶接線の液体浸透探傷検査による線状指示模様及びデジタル顕微鏡観察による微細な穴状模様が確認され、ヘリウムリーク検査により漏えい箇所と評価した場所を包含した範囲(縦約450mm×横約1450mm)を原因調査試験片として切り出し後、社外研究施設へ搬出しました。(添付−1参照)
調査は原因調査試験片のうちヘリウムリーク検査で漏れの確認された部位(調査試験片)について調査を進め、その後、調査試験片周辺(予備試験片)について同様の調査を実施しました。
(添付−2参照)
1.1 調査方法
調査は、非破壊検査およびヘリウムリーク検査で漏えい箇所を特定し、特定した漏えい箇所に対し貫通部の断面等の詳細観察を行い原因の究明を行うこととしました。
(添付−3参照)
1.2 調査試験片の漏えい欠陥部特定調査結果
(1)外観観察
調査試験片の外観検査を実施した結果、溶接線に現場で確認された微細な穴状の模様は、微細な穴状の欠陥であることが確認されました。
(2)非破壊検査による調査試験片の内部調査
放射線透過検査および超音波探傷検査では漏えいにつながる漏えい欠陥の確認はできませんでした。
放射線透過検査では、溶接金属中に生じた小さな球状の空洞(ブローホール※1)による7箇所の球状指示や、溶け込み不足と考えられる6箇所の線状指示が確認されました。
また、超音波探傷検査では、7箇所の指示が確認されており、この指示は、放射線透過検査の指示とほぼ一致していました。 (添付−4参照)
※ 1 ブローホール:溶接中に発生したガスにより生成した空洞
(3)ヘリウムガスを用いた発泡及びリーク検査
漏えい場所の特定調査中にプール水の出水が停止したことから、プール水中の浮遊物が漏えい欠陥部に詰まったことによるものと考えました。
このため、漏えい欠陥部の閉塞物を除去するため、調査試験片の洗浄等を行った後、ヘリウムガスを用い発泡検査及びヘリウムリーク検査を実施しましたが、いずれの検査でも漏えい欠陥部の確認はできませんでした。
上記の非破壊検査及びヘリウムリーク検査では、漏えい欠陥部の確認ができなかったため、調査方法を見直し、以下のとおり調査を進めました。(添付−3参照)
(4)調査試験片を削り込みによる漏えい欠陥の特定調査
調査試験片から下地材を取り外した後、調査試験片の表面及び裏面から削り込みを行い、液体浸透探傷検査後、光学顕微鏡で拡大観察(20及び100倍)を実施し、有意な欠陥の絞り込みを行いました。
[1] 表面側からの調査
表面側から約0.4mmの深さまで削り込みを実施し、溶接線上端部分に、穴状欠陥(最大直径0.5mm)を3箇所確認しました。(添付−5参照)
[2] 裏面側からの調査
裏面側から、約0.5mmの深さまで削り込みを実施し、液体浸透探傷検査で溶接部境界付近に穴状及び線状の欠陥を確認しました。更に光学顕微鏡での拡大観察の結果、微細なひび状欠陥を確認しました。(添付−6参照)
[3]溶接断面側からの調査
漏えい欠陥を特定するために、3箇所に絞り込まれた表面欠陥とその裏側の近傍に存在する欠陥に着目して、断面観察試験片(I、III、IV)を作成し、試験片溶接部の断面方向から、精密な削り込みと詳細な表面観察を繰り返すことにより、漏えい欠陥部の確認を進めました。(添付−7参照)
断面観察試験片(I、III、IV)では、調査を進める過程で、溶接部の裏面に、溶接時の溶け込み不足、ライニングの仮付け溶接部の溶接金属と母材の境界に未溶着と考えられるすき間状の開口部やブローホールが観察されました。
また、断面観察試験片(III)の溶接金属と母材の未溶着と考えられる開口部近傍の微細なひび状欠陥1箇所からは、粒界・粒内割れが観察されました。
しかし、これら表面及び裏面に観察されたいずれの欠陥もライニング厚さに対して浅く(最大深さ約1.5mm)漏えい欠陥と直接結びつくような欠陥ではないことが判明し、漏えい欠陥の確認、原因の解明には至りませんでした。
(添付−8参照)
(溶け込み不足については、仮付けの溶接金属が母材と溶着しなかった部分と考えられますが、仮付けした後に二層溶接していることから問題なく、また、ブローホールは溶接内部に生成した空洞であり、亀裂や侵食孔の起点となるものではありません。)
[4]裏面側の微細なひび状欠陥の調査
漏えい欠陥の特定調査とは別に、裏面側に観察された微細なひび状欠陥を詳細に調べるため、代表的に断面観察試験片(II)を作成し、削り込みと表面観察を実施しました。
(添付−7参照)
調査の結果、裏面側の微細なひび状欠陥は、溶接時の溶け込み不足又は仮付け溶接部の未溶着と考えられる開口部であることがわかりました。(添付−9参照)
なお、上記の調査で観察された微細なひび状欠陥については、長期的に見たライニングの健全性の観点から、今後も社外研究施設でさらに詳しい調査を行うこととしています。
1.3 予備試験片の漏えい欠陥部の特定調査結果
調査試験片に対するヘリウムリーク検査では、漏えい欠陥箇所が確認できなかったため、溶接線を含む予備試験片も調査対象として、調査試験片と同様にヘリウムリーク検査、試験片の削り込みによる漏えい欠陥の特定調査等を実施しましたが、漏えい欠陥部は確認できませんでした。
1.4 漏えい欠陥を特定できなかった原因評価
調査試験片は、現地において、液体浸透探傷検査で有意な指示模様が確認されたので、貫通欠陥部を特定するために真空箱検査を実施しましたが、発泡は確認されませんでした。このため、表面を拡大観察したところ、微細な穴状模様が確認されたため、当該場所においてヘリウムリーク検査を実施し、その結果、ヘリウムの漏えいが確認されたことから、漏えい場所であると評価したものです。
今回、この漏えい場所と評価するに至った各検査方法を再評価した結果、以下の改善すべき点が明らかになりました。
(1)液体浸透探傷検査
液体浸透探傷検査前には被検査面を十分に乾燥し、水分を除去する必要があります。現地では温風機により乾燥を行いましたが、工場でモックアップ試験を行った結果、今回現地で適用した温風機では、被検査面の温度が24℃
→ 29℃までしか上昇せず、欠陥内部に水分があった場合、十分に除去できず欠陥検出性の低下をまねく可能性があることがわかりました。
(2)ヘリウムリーク検査
ヘリウムリーク検査においては、測定環境に存在するヘリウムの影響を受けないように実施する必要があります。現地において実施した測定方法を工場のモックアップ試験で確認した結果、検査箱のシールが一重であるため、測定環境に存在するヘリウムが検査箱内に漏れ込み、誤検出する可能性があることがわかりました。
1.5 今後の調査の進め方
前述の液体浸透探傷検査及びヘリウムリーク検査の再評価にもとづき、以下のとおり調査方法の見直しを行い、改善した方法でPWR燃料貯蔵プール北壁部西側ライニング部溶接線を徹底して再調査することとしました。(添付−10参照)
(1)液体浸透探傷検査の改善点
・欠陥内部に水分があることを考え、検査対象面を100℃以上に加熱し、十分な乾燥を行なうとともに、揮発性のアセトンで付着物や汚れを除去します。
・さらに、浸透時間及び現像時間を15分から1時間、10分から2時間に長時間化し、指示模様をより見やすく、検知しやすくします。(添付−11参照)
(2)ヘリウムリーク検査の改善点
・検査箱内への測定環境からのヘリウムの漏れ込みを防止するため、検査箱のシールをニ重にして、シール間に窒素を封入します。
・ヘリウムガス以外のガスの影響を排除するため、ガスを凝縮して除去する装置を設置し信頼性を向上させます。 (添付−12参照)
現場の再検査により漏えい箇所が特定された場合には、社外研究施設へ搬出し漏えい欠陥の特定、漏えい原因の調査を実施します。
2.微細な穴状模様の調査結果
2.1 プール水等の微生物調査結果
プール水の原水として使用している河川水並びにPWR燃料貯蔵プール床面のプール水及び付着物から、腐食に関与する微生物を確認しました。(添付−13参照)
2.2 微細な穴状模様の拡大観察結果
プール下部横溶接線上に観察された微細な穴状模様は、表面から約0.2mm削り込むことにより全て消滅し、浅い欠陥(0.2mm以下)であることが判明しました。これは、現地で採取したレプリカ(表面の状態を樹脂等を用い写し取ること)の調査結果と良い整合がありました。(添付−14参照)
また、予備試験片に観察された微細な穴状模様部を電子顕微鏡で拡大観察したところ、穴状模様部の底部表面に、腐食によると考えられる微細な凸凹が確認されました。(添付−15参照)
2.3 微細な穴状模様の発生原因と対策
微細な穴状模様の発生原因は、プール水は通常の局部腐食(孔食、すき間腐食)を発生させる水質環境にないのにも係わらず、
a)電子顕微鏡観察により腐食と考えられる微細な凹凸が確認された
b)観察された凹凸は微生物腐食の特徴とされる特定組織の選択腐食によるものと考えられた
c)原水及びプール水に腐食に関与すると考えられる微生物の存在が確認された
ことから、微生物腐食によるものと判断しました。
今回調査した範囲では、微細な穴状模様は0.2mm以下と浅いものであり直ちライニングの健全性に影響を与えるものではないと考えますが、長期的なライニングの健全性の視点から、プール水の殺菌、河川水からの取水時殺菌の見直し、プール水の定期的な微生物分析等の対策について、有効性及び安全性を評価し、実施します。
3.その他の調査結果
3.1 成分分析の結果
材料健全性を確認するために、以下の成分分析を実施しました。また、これらの結果は、今後の再調査結果等と総合し、漏えい原因の評価に活用します。
(1)ライニング材、溶接部及びコンクリート組成分析
ライニング材、溶接部、コンクリート成分分析の結果、規定値を満足していることを確認しました。
(2)ライニング材裏面の塩素分析
施工時の基準70(mg/m2)に対して、最大で7(mg/m2)※2の塩素濃度であり、基準値を十分下回っていることを確認しました。
※2 塩素の分析はライニング材裏面の付着物をふき取り、イオンクロマト法により定量した
3.2 プール床面北西コーナー部茶褐色斑点模様の調査結果
プール水位低下作業が終了し、燃料貯蔵ラックの取り外し後にプール北西コーナー床面で確認した茶褐色斑点模様は、今回の調査のためにプール内部の清掃用に事業所外から持ち込んだ吸引洗浄装置※3の内部に残留していた工場試運転時に使用した微細な鉄球(ピーニング用ショット)が、排出され、腐食状態で見つかったものであることが判明しました。
(添付−16参照)
※3 吸引洗浄装置:燃料貯蔵ラックの移動に備え、ラック上部等の吸引洗浄のために使用した装置
3.3 結露水の発生抑止対策と効果の確認結果
例年、夏季は結露の多くなる六ヶ所特有の霧の季節ですが、現在、漏えい検知管からの出水がないことを確認しています。
今後も引き続き監視を行い、効果の確認を継続します。
(建屋コンクリートとライニングとの隙間に発生する結露水を抑止するため、以下の対策を実施しました。
[1] 空気の流れを引き起こす燃料貯蔵プールエリア(地上1階)と漏えい検知装置設置エリア(地下3階)との空気差圧を解消するための換気系の調整。(4月30日終了)
[2] 建屋コンクリートとライニングとの隙間への空気流入口を、シール材で閉止する恒久対策。(4月22日終了)
なお、漏えい原因調査のためシートで仮養生を行っているPWR燃料貯蔵プールについては、作業の終了後に恒久対策を実施します)
添付図版一覧
(クリックすると大きい画像がご覧になれます)
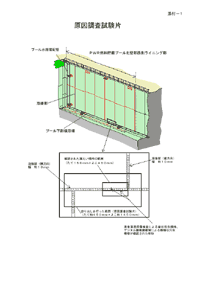
添付-1
|
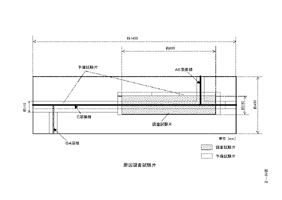
添付-2
|
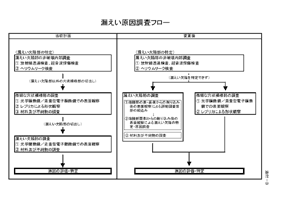
添付-3
|
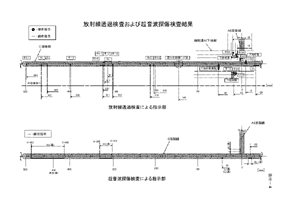
添付-4
|
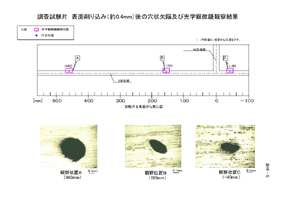
添付-5
|
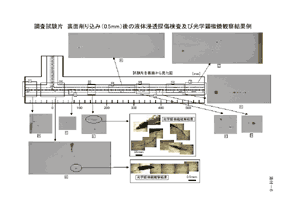
添付-6
|
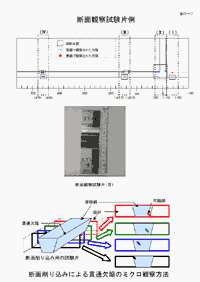
添付-7
|
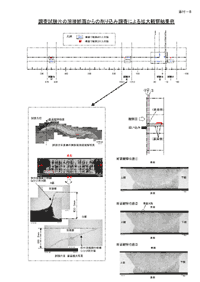
添付-8
|
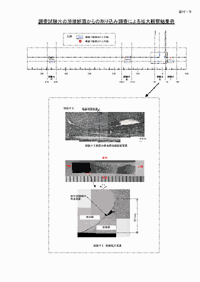
添付-9
|
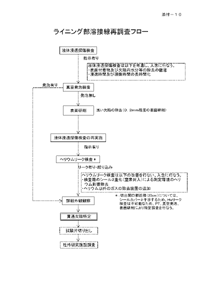
添付-10
|
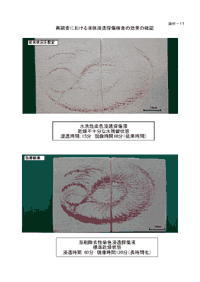
添付-11
|
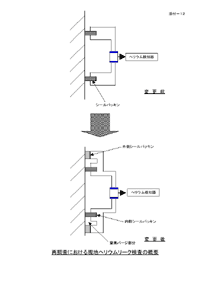
添付-12
|
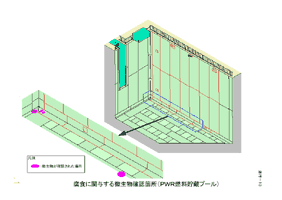
添付-13
|
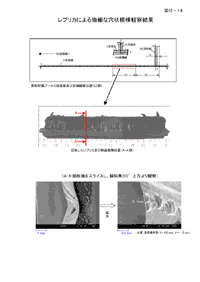
添付-14
|
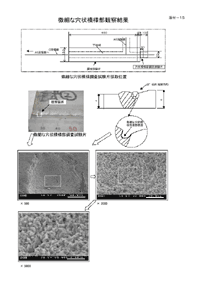
添付-15
|
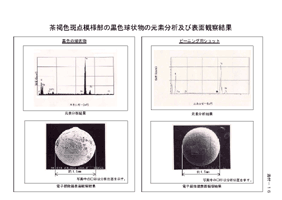
添付-16
|
|